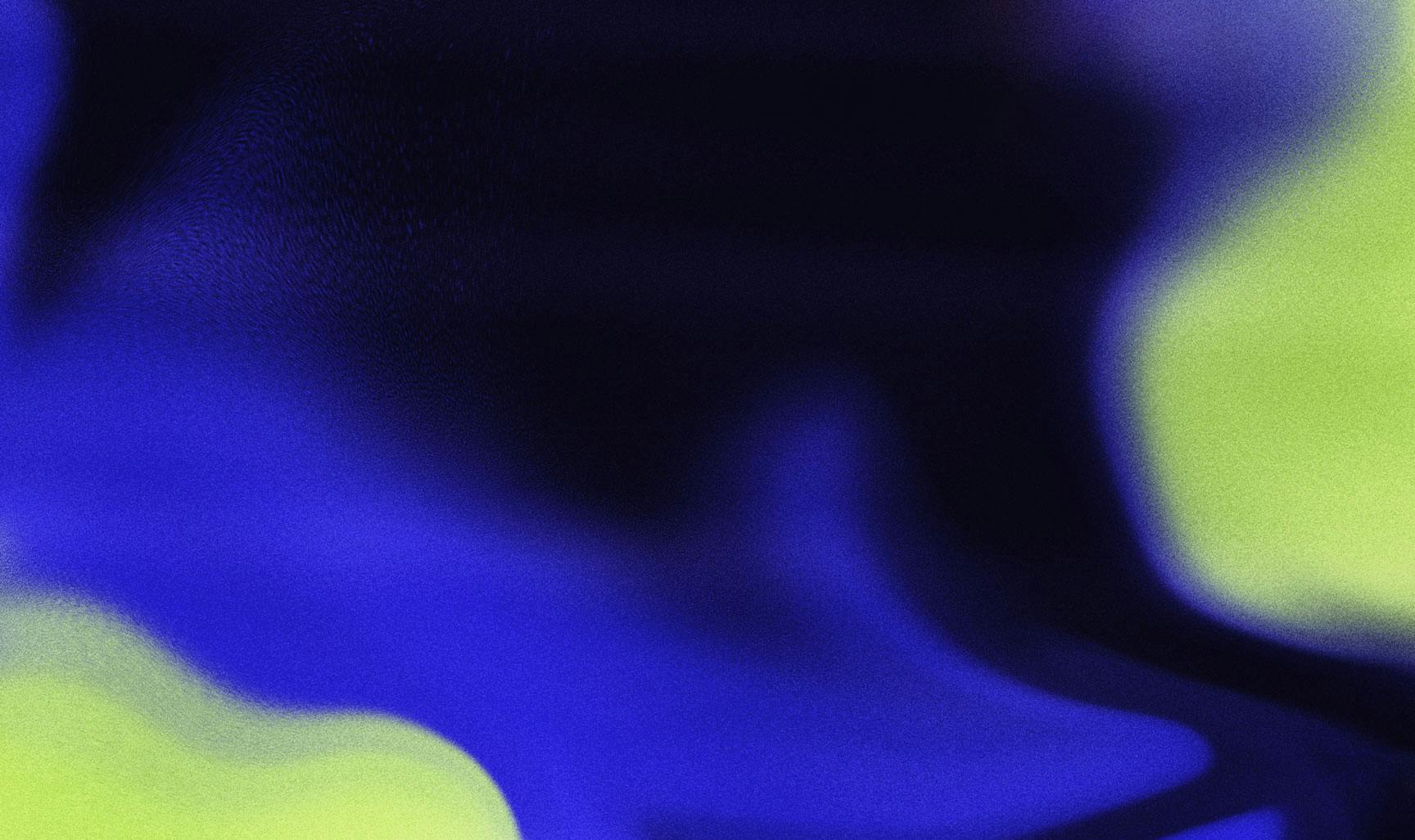
Insights
Check-out the no-nonsense insights from a no-nonsense business.
Digitalization & New Technologies
Software Defined Automation (SDA): harnessing the power of software for automation development
In today’s fast-paced digital world, automation has become a crucial aspect of businesses across various industries. From cybersecurity threats to the need for open systems, companies are con-stantly seeking innovative ways to streamline their processes and increase efficiency. This is where Software Driven Automation (SDA) comes into play.
Latest insights
Digitalization & New Technologies
Software Defined Automation (SDA): harnessing the power of software for automation development
Digitalization & New Technologies
Driving the Development of Alternative Fuels Services: 6 Industry Drivers
Operational Efficiency
5 things to Consider When Choosing an R&D Partner: Have You Faced These Challenges?
Digitalization & New Technologies
Preparing a Factory and a Production Plant for Success in the Evolving Energy Landscape
Digitalization & New Technologies